
The integrally punched-out or cut carrier film sheet may be referred to as “separator,” rather than “carrier film sheet” because it is not serving as a transport medium. The optical film sheet thus punched or cut is produced by integrally punching or cutting not only the surface-protection film but also the carrier film protecting the exposed surface of the adhesive layer in the polarizing composite film. The punching or cutting of the optical film into the rectangular-shaped sheet may be collectively referred to as “individualized sheets” or “a method and system for manufacturing individualized sheets” for liquid-crystal display elements. The width or the short side dimension of the optical film sheet to be processed into the rectangular shape is smaller than the width of the optical film. This is described in Japanese Laid-Open Patent Publication No. Therefore, in a polarizing sheet for use in producing a liquid-crystal display element of a TN-type liquid-crystal panel, it is required that the optical film is punched or cut into a rectangular-shaped sheet having a long side or a short side determined in accordance with the size of the TN liquid-crystal panel, and inclined by 45 degrees with respect to the orientation direction of the polarizer produced by stretching in the lengthwise or widthwise direction. It is therefore necessary that the polarizing sheets made from the polarizing composite films to be laminated respectively on the front and back sides of the liquid-crystal panel with polarizers respectively oriented in directions inclined respectively by 45 degrees with respect to a lengthwise or widthwise direction of the display screen so as to conform to the rubbing directions. However, in the case where the LCD is designed to allow images as seen from right and left sides of a display screen as those view from directly in front of the display screen, the direction of rubbing on the orientation film at the viewing-side must be 45 degrees (the rubbing direction of the other orientation film being 135 degrees). This means that the liquid-crystal molecules are twisted by 90 degrees along the optical axis, so that when a voltage is applied, the liquid-crystal molecules are aligned in a direction perpendicular to the orientation films. Although a technical explanation is omitted, in an LCD using such TN-type liquid-crystal panel, liquid-crystal molecules are provided between two upper and lower orientation films having respective rubbing directions on the inner surfaces of the substrates of the liquid-crystal panel. Recently, LCDs using a VA (vertical Alignment) type liquid-crystal, an IPS (Inplane Switching) type liquid-crystal etc., were put into practical use. In liquid-crystal display element technologies, LCDs using a TN (Twisted Nematic) type liquid-crystal were the first to be put into practical use.
#Manufacturing defect process flow chart pdf#
PTO PTO PDF Espaceįor a liquid-crystal display element to function, the direction of orientation of liquid-crystal molecules and the direction of polarization of the polarizer must be set in a particular relation to each other. The optical film laminate having a carrier film releasably laminated to an adhesive layer, wherein defect-free normal polarizing sheets and a defective polarizing sheets are formed on the carrier film by forming slit lines corresponding to above regions along the transverse direction of the optical film laminate. The optical film laminate having defect-free regions having a predefined length corresponding to the dimension of a liquid-crystal panel and defective regions having a predefined length different from the defect-free region, based on the detected position of defects.
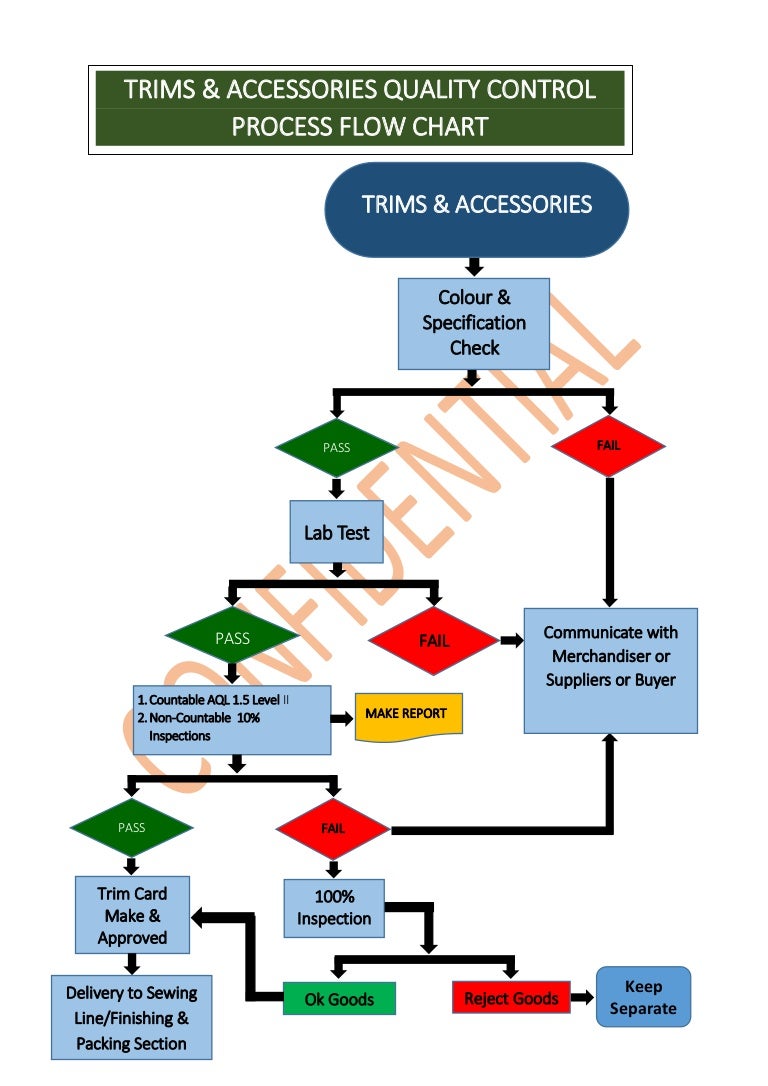
The optical film laminate formed as a continuous web with the predefined slit lines for use in a continuous manufacturing system by laminating optically functional film sheets to liquid-crystal panels. An optical film laminate that has predefined slit lines for enhancing both product accuracy and manufacturing speed in liquid-crystal display element manufacturing to radically improve manufacturing yield.
